Symposium for mineral processing technology 2023
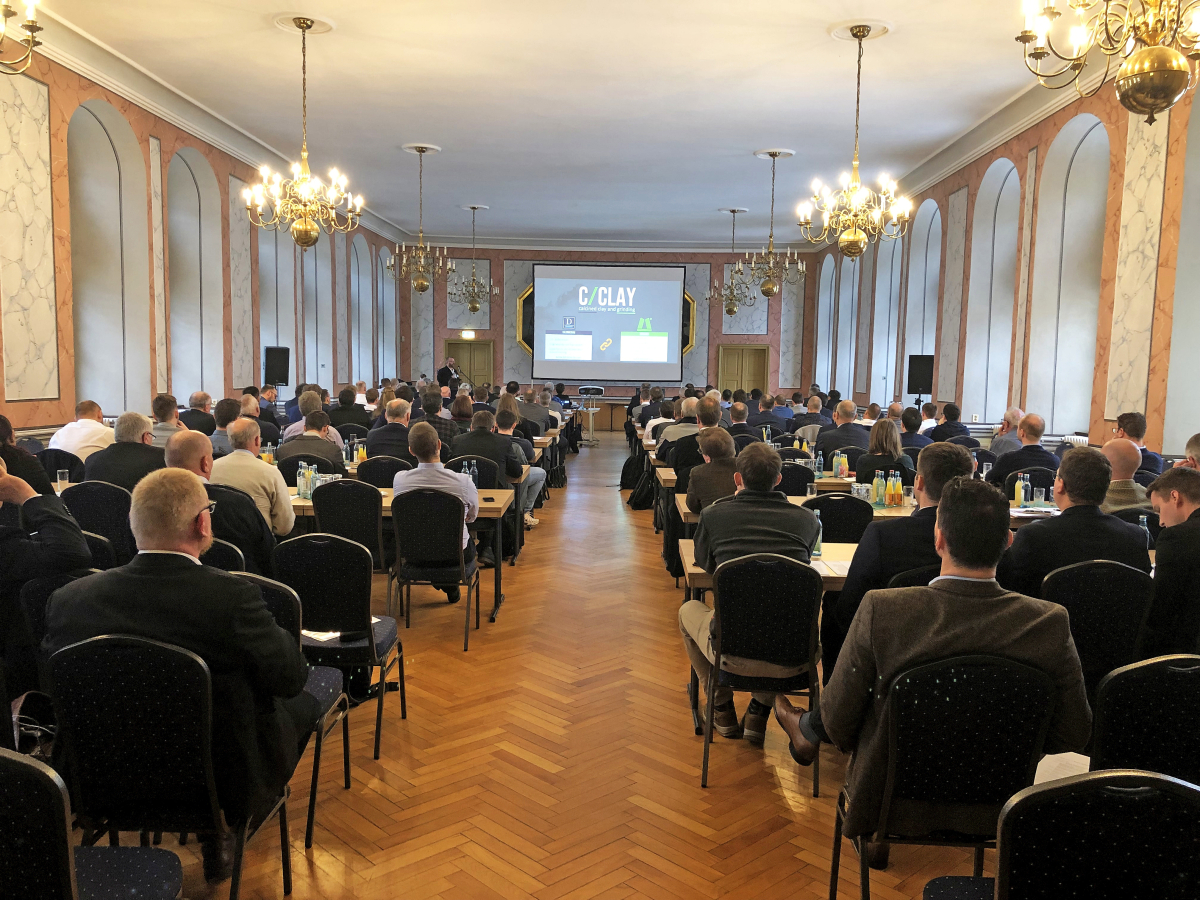
© Dr. Petra Strunk
The symposium participants were welcomed by Florian Festge, Haver & Boecker OHG and Chairman of the Friends and Sponsors of the Institute of Mineral Processing and Recycling Systems Technology, and Prof. Dr. Holger Lieberwirth, from the Institute of Mineral Processing and Recycling Systems Technology, with brief overview contributions.
This was followed by the plenary lecture by Dr. Simone Schulze, VDZ Technology gGmbH, on the topic of “Calcined clays from gravel and sand deposits for cement”. The cement industry is currently undergoing a far-reaching transformation process. The main focus is on reducing CO2 emissions. One lever is the reduction of the clinker factor. However, hard coal fly ash and granulated blast furnace slag will no longer be available in sufficient quantities in the future. The use of calcined clays in particular is currently favored. However, large-scale production is still in its infancy. Current investigations are focusing on the reactivity of calcined clays from different raw material sources.
“Technical solutions for separating and dewatering clayey components from processing water in sand/gravel opencast mines” was the topic of the presentation by Ferdinand Doppstadt, LIG GmbH. The problem with gravel processing is the treatment of the process water so that it can be recirculated. Various state-of-the-art methods for separating water/sediment and dewatering the sediment were presented and discussed.
“Challenges and progress in the mineralogical analysis of raw and residual materials containing clay minerals” – Dr. Reinhard Kleeberg from the Institute of Mineralogy at the TU Bergakademie Freiberg devoted himself to this challenging topic. X-ray diffraction has been used to analyze clay minerals for over 100 years, as chemical analysis methods are not suitable. However, there are also complicating conditions here, for example, the clay minerals are structurally closely related to each other and can therefore only be distinguished in certain details in the diffractogram, or the clay minerals exhibit misordering, which reduces the information content of the diffractograms. In addition, there is no standardized procedure for sample preparation and measurement. In this lecture, all these problems were addressed and realistic modeling of the diffractograms for structurally disordered clay minerals was presented.
The following presentation also dealt with the production of calcined clays as clinker substitutes. The topic “Clay calcination - from research to practice” was presented by Dr. Martin Reformat from Loesche GmbH. The focus of Loesche GmbH’s research and development is on producing a product that is optimized in terms of both energy and process engineering, with the process engineering steps of conveying, pre-crushing and crushing, firing, cooling, grinding, mixing and packaging being examined in more detail.
The following two papers dealt with the topic of recycling. In “Jigging machines in concrete recycling, applications and operating experience”, Thomas Neumann from allmineral Aufbereitungstechnik GmbH discussed the frequently used processing methods of crushing, classifying and sorting and then looked in particular at the possibilities and applications for sorting concrete demolition or construction waste using air-pulsed jigging machines. The presentation by Dr. Jan Lampke and Benjamin Gurra from Haver Niagara GmbH on “Lets keep the planet blue – practical examples from the recycling of slag, dust and sludge” examined the different crushability of brittle slag and ductile metal particles for material separation using innovative crushing and screening technology. Agglomeration is also used in non-ferrous and ferrous metallurgy for the sustainable utilisation of accumulated dusts.
Increasing digitalization is also reflected in processing technology. “SMART. SAFE. SUSTAINABLE. – How digital products are changing mobile processing technology” was the exciting topic presented by Tobias Böckle from Kleemann GmbH. The processing of mineral waste into secondary raw materials is a particular challenge due to the increasing documentation effort, higher quality and safety requirements and, on the other hand, a shortage of qualified specialists. Kleemann offers its customers numerous digital solutions that support users in their daily work. Digital continues. Dr. Eric Fimbinger, Chair of Mineral Processing and Refining at the University of Leoben, and Philipp Falkner from RM RUBBLE MASTER HMH GmbH presented the targeted use of numerical simulation for successful digital system development in modern mineral processing technology in “Digital system development in mineral processing technology – virtual behavioral analysis using the example of the RM Active Grid”. Automation, here in the field of grinding technology, is also the keyword of the next presentation by Moritz Pultke from BHS-Sonthofen GmbH: “Development of an automated control strategy for rotor impact mills”. A concept for the automatic detection of the current grinding gap and quantification of the hammer states was presented. A CPA sensor (Computerized Particle Analyzer) from Haver & Boecker was used for the automatic analysis of the particle size distribution. As a result of these investigations, control concepts of varying complexity were developed.
This was followed by topics from the practice of mechanical processing. Dr. Jörn Matschke and Karsten Kochte from Actemium BEA GmbH presented an automated system for the quality management of coal in “Bulk material tracking and process modeling of a continuous belt conveyor system with mixing and storage area – quality management of the overall system using the example of a coal mine in Kazakhstan”. The specified goal was not to exceed an ash content of 42 % in the product.
The presentation “DEM simulation of crushing processes in sizers with the TAKRAF crushing model” by Dr. Marko Schmidt, TAKRAF GmbH, dealt with the new X-TREME CLASS SIZER product line and with DEM simulations in order to design the sizer specifically for the respective application and to be able to operate it economically even under difficult conditions.
Although the same processing systems are used in mining and the construction industry, the requirements placed on the machines differ considerably. In the presentation “Different requirements for processing machines in the ‘mining’ and ‘construction’ sectors using the example of screening machines” by Andreas Kanter, Metso Outotec Germany GmbH, the requirements for screening machines in both application areas were presented and different machine concepts were derived from this.
The lecture program concluded with the contribution “Energy saving through dry grinding with roller mills” by Dr. Felix Heinicke from Köppern Aufbereitungstechnik GmbH. This paper looked at the energy calculations and effects of the BONUS on various grinding circuits for cement and ore applications. The day ended with an evening event in the Ratskeller Freiberg.