Truck unloader for fast loading of bulk material
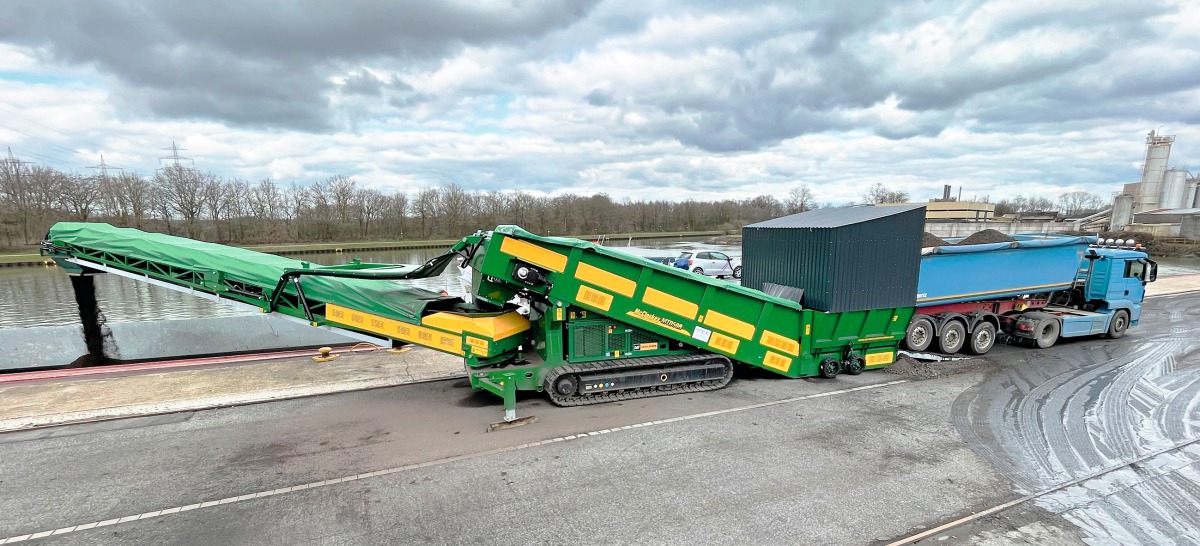
© APEX Fördertechnik The efficiency of cargo handling for ship transport is primarily determined by the speed of the loading process, as the demurrage times in the port represent a significant cost factor. Usually, original bulk materials such as recycling material, sands, gravels or coal are dumped close to the berth in order to load them onto a cargo ship in a separate work step using cable dredgers, which is time-consuming. Material handling with a crane dredger has proven to be relatively impractical due to the comparatively high cost and operating effort.
2 The length/height of the track-mounted Truck Unloader MTD50R with retracted discharge conveyor is 19.8 m / 3.6 m – in operation its working length is 27.9 m with a variable height of up to 7.9 m
© APEX Fördertechnik
With the MTD50R Truck Unloader from McCloskey, Apex Fördertechnik supplies a conveying device that is able to take bulk materials directly from a semi-trailer and load it onto a cargo ship in one operation. “We have already run numerous tests with McCloskey to fundamentally simplify the transfer of goods from land to water,” explains Rolf Lieben, Managing Director of Apex Fördertechnik from Geilenkirchen. “One of our customers then expressed the concrete goal of using this mobile conveyor system to load 300 t of asphalt rubble per hour from a truck onto a cargo ship. As a result, our test runs with the new MTD50R Truck Unloader showed that even a reloading of between 450 and 500 t of feed material per hour is possible. This result not only clearly exceeded the stated target, but in fact doubled the amount of feed material that would otherwise be achieved in an hour with a conventional cable dredger. In this way, the demurrage time of the cargo ship can effectively be halved.”
Without having to dump material at the dock first and then pick it up again, reloading via Truck Unloader offers a considerable time advantage. The mobile conveyor is positioned directly at the dock, the semi-trailer reverses up to the machine and loads the material directly into the feed hopper. The heavy-duty steel hopper is 2.20 m wide and can hold up to 20 m³ in the standard version. The swivelling and extendable discharge belt allows the feed material to be loaded far into the ship as required – even lowering the conveyor belt to up to 10 ° is possible here to maximise the reach. Taking into account local peculiarities such as unusual railing heights or extreme water levels, the discharge belt can also be raised to a discharge height of up to 6.50 m. A catch basin located underneath the system prevents bulk materials from falling out in an uncontrolled manner.
“Our customers’ response to the MTD50R Truck Unloader from McCloskey has been consistently positive. On the one hand, this is due to the high throughput resulting from the low unloading times of only 3 min. per truck, and on the other hand, we have equipped the unloader with additional devices in individual cases at the request of individual customers, which ensure a high level of safety,” explains Lieben. “Starting with the installed lower belt protection to prevent material from falling into the water during loading, to an enclosure with a tarpaulin over the loading area, to spraying devices at the transfer points – in case it is particularly dry.”