Secondary use of mineral raw materials
Summary: Due to the CO2 problem, the production volumes of metallurgical slags and fly ash, furnace bottom ash and FGD gypsum from coal-fired power plants are stagnating or even declining in many important countries. On the other hand, demand is increasing in key customer industries, as these secondary raw materials provide economic, energetic and environmental benefits. This report provides background information on this situation, as well as facts and figures.
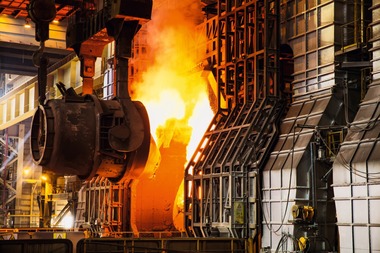
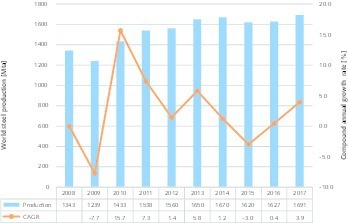
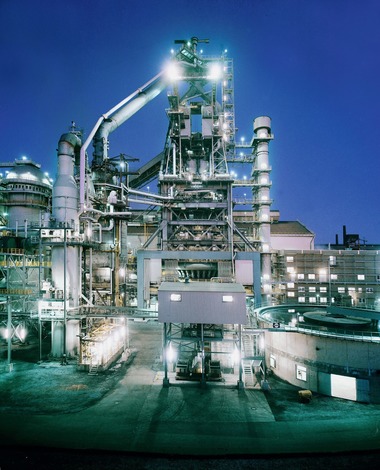
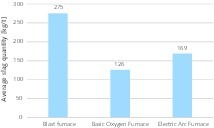
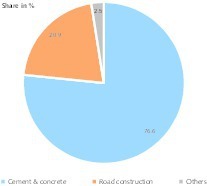
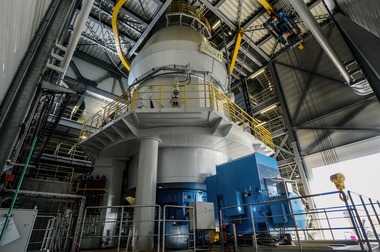
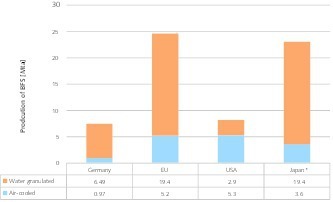
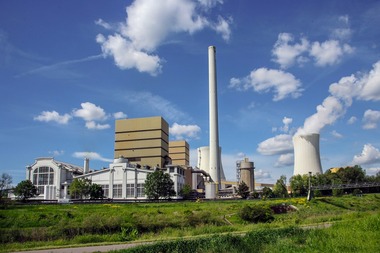
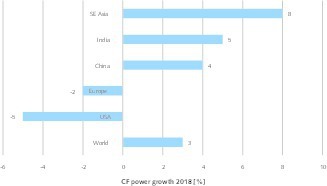
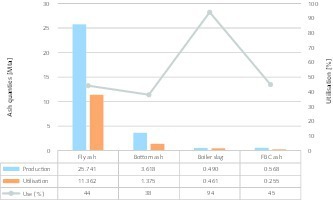
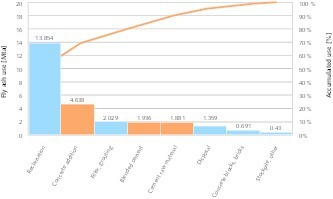
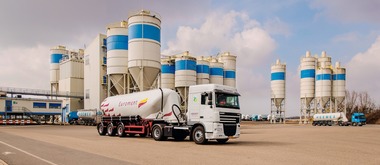
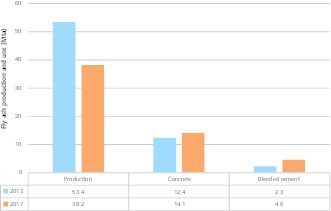
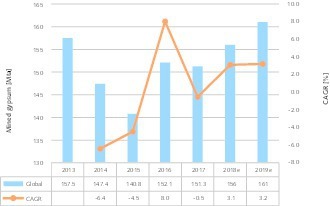
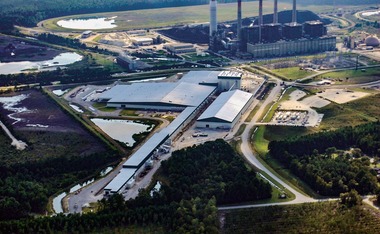
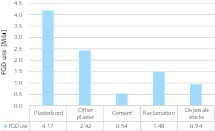
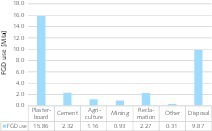
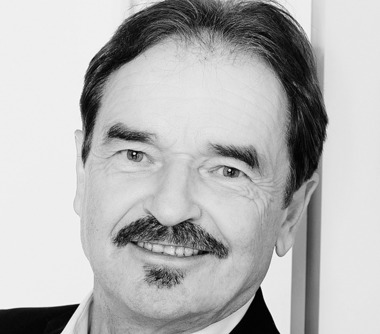
1 Introduction
The use of industrial mineral by-products as a secondary raw material has a long tradition. In Germany, blastfurnace slag from pig iron production has been used in the production of bricks since 1865 and, since 1879, for the production of cement. In Japan, these findings were first applied in 1910 [1]. In the power plant sector, flue gas cleaning with dedusting systems became established in the middle of the 20th century. Also, the first electrostatic precipitators were used to remove the fly ash from flue gases. In Germany, as one of the pioneering states, flue gas desulphurisation has also been mandatory for new coal-fired power plants since 1974, providing the basis for so-called FGD gypsum (FGD = flue gas desulphurisation) [2]. Since then, more than 50 years have passed and the use of these industrial by-products has not only gained in importance, but has also changed significantly.
Today, granulated blast furnace slag, fly ash and FGD gypsum are still used primarily in the building materials industry. Quality parameters are crucial prerequisites for the approval and use of minerals in these industries. If the respective substances do not receive the appropriate approval, for example if the loss on ignition or the CaO content is too high or if the proportion of metals and interfering trace elements exceeds limit values, then they are generally used in downstream applications such as road construction or for landfilling. The licensing practice and utilisation rates in the building materials industry vary from region to region and country to country. Blast furnace and ash cements are standardized. The highest slag content of up to 95 % is possible for CEM III cements. With building inspectorate approval, hard coal fly ash, for example, can be used in concrete with factors of 0.4 to 0.7 relative to the cement content, depending on the grade.
Crucially, the quality of blast furnace or ash cements is not lower than that of other Portland cements. Indeed, the properties of such cements or concretes may even be superior. Blastfurnace cement, for example, is more resistant to salts and has a lower heat of hydration, which is particularly advantageous when it is used for the solid structural elements of underground constructions and hydraulic structures. Fly ash, for example in fresh concrete, improves the flowability, workability, pumpability and compressibility and reduces the heat of hydration, the water requirement, the sedimentation and voids formation. Last but not least, the use of such cements and concretes in which the clinker from cement production is substituted by secondary materials significantly reduces the manufacturing costs and the CO2 emissions [3].
2 Use of iron and steel slags
Iron and steel slags comprise blast furnace and steelworks slags. Blast furnace slag is produced at about 1500 °C during the reduction process in the blast furnace from the accessory minerals of the iron ore and from the added slag formers, such as limestone and dolomite. If the slag is cooled slowly in the air, crystalline blast furnace slag (BFS) is produced and if it is cooled rapidly with water, slag sand or granulated blast furnace slag (GBFS) is produced. Steelmaking slag is produced as a molten mass during the processing of pig iron, sponge iron or scrap iron into steel. It is formed from the oxidized accessory elements of the pig iron or other metallic charge materials, as well as from the lime or burned dolomite that is added for slag formation.
World crude steel production increased from 40 million tonnes per year (Mta) in 1900 to 1691 Mta in 2017 (Fig. 1). The increase in production volumes, however, has been repeatedly interrupted in recent years, for example in 2009 as a result of the global economic crisis and in 2015 as a result of the falling demand in China. Future medium-term forecasts for steel production assume moderate growth of 2.5 % to 3.0 %, after even higher growth rates were considered possible a few years earlier. The proportion of blast furnace pig iron (Fig. 2) fell slightly in 2008 from 70.6 % to 69.8 %. China alone accounts for 60.2 % of blast furnace pig iron, while Europe (EU28) has a share of 7.9 %, the rest of the Far East including India has a share of 17.9 % and North America accounts for 2.8 % (all data apply to 2017).
Differing information exists about the amount of slag produced by the steel industry. The quantities from blast furnace operations, for example, have drastically declined from around 800 kg/t of pig iron to less than 300 kg/t in the past 50 years. With the current state of the art, about 250 – 275 kg of slag per ton of pig iron (in some cases up to 400 kg/t) and about 120 – 170 kg/t of steelmaking slag are produced. Fig. 3 shows average values published by EUROSLAG (The European Slag Association) for the specific slag production from the main processes for pig iron production and steelmaking. The chemical composition of the slag depends on the specific steelmaking process and on the aggregates used and differs in its proportions of lime, silicate, iron and phosphate.
Given the current worldwide production of pig iron, the slag quantities from blast furnaces alone presumably exceed 325 Mta. In Europe (EU28), about 91.3 Mta of pig iron were produced in 2016. The produced quantities of slag were analysed for 93 % or 85.3 Mta respectively. Of the 24.6 Mta of blast furnace slag, 19.4 Mta (78.9 %) were granulated and 5.2 Mta (21.1 %) were air cooled. As shown in Fig. 4, 76.6 % of the blast furnace slag was used for cement and concrete production, 20.9 % served as a base course for road construction and 2.5 % was used for other purposes. Of the analysed 18.4 Mta of steelmaking slag produced in the EU28 in 2016, 14.2 Mta (77 %) were utilised. A total of 4.4 % went to the cement and concrete industries (as a raw material and substitution product), 46 % were used for road construction, 15.3 % went to the metallurgical industry, 11.5 % to other uses and 22.7 % to intermediate storage or landfill.
In the case of blastfurnace slag, its utilisation depends primarily on whether the slag is granulated or not. Granulated blast furnace slag (slag sand) can be used 100 % in the cement and concrete industry. For this purpose, the slag is finely ground (Fig. 5). The product generates revenues of the same order of magnitude as cement clinker. Fig. 6 depicts the quantities and proportions of granulated blast furnace slag produced in the EU, Germany, the USA and Japan. The figure shows that Germany and Japan account for the highest proportions of granulated slag with 87 % and 84 % respectively. The EU accounts for a high 79 % share, with France and Belgium considered as leaders next to Germany. By contrast, the US only accounts for 35 % and meanwhile has to import blastfurnace slag, as do many countries in the Middle East and Africa.
3 Use of fly ash and furnace bottom ash
The quality and utilization possibilities of ash and other by-products produced in coal-fired power plants depend on the type of coal used and on the combustion process. The highest quality fly ash and bottom ash are produced in coal-fired power plants with dry furnaces (Fig. 7). Also of high quality are boiler slag granulates, which are produced during the combustion of hard coal in slag tap furnace firing systems. Ashes from lignite-fired furnaces are of inferior quality, since these can contain high proportions of CaO and undesirable trace elements. The lowest-quality products are fluidised bed ashes (FBC) from fluidised bed firing systems for burning lignite, wood, sewage sludge, etc., as well as spray absorption products from flue gas cleaning systems employing the spray absorption process.
Coal still accounts for 38 % of global energy production. According to information from the IEA (International Energy Agency), the figure of 10 000 TWh of generating capacity was exceeded for the first time in 2018. However, as a result of the CO2 problem, drastic global reductions in coal-fired power generation are expected by 2040. The aim is to reduce the proportion of coal-fired electricity generation plants without CO2 capture and storage to only 5 % by 2040. At the present time, however, the amount of coal-fired power generation is still increasing, especially in Asia (Fig. 8). In 2018, the biggest growth rate was in Southeast Asia with 8 %, followed by China and India with 4 % and 5 % respectively. In Europe and the US, numerous coal-fired power plants have been shut down, which means reductions in growth and in the resulting amounts of produced ash.
The produced quantities of fly ash and bottom ash from coal-fired power plants depend on various parameters. Crucial factors are the ash content and calorific value of the coal, but also the boiler efficiency, since with a higher efficiency a specifically smaller quantity of coal has to be used. Typical ash contents vary between 10 % and 35 %, depending on whether the coal being burnt is low-ash steam coal (imported coal) or high-ash local steam coal (e.g. in India), containing up to 55 % ash. For Western Europe (EU15), Fig. 9 shows the amount of different ashes and slags produced in 2016, as well as the corresponding quantities utilised [4]. Fly ash accounted for 25.7 Mta (84.6 %) and boiler ash for 3.6 Mta or 11.9 % of the produced quantities. The utilisation rates of fly ash are 44 %, of bottom ash 38 % and of boiler slag granulate 94 % (used as an abrasive). Also, fluidised bed ash still finds a utilisation rate of 45 % as a filler material.
Fig. 10 shows the proportion of fly ash utilised in higher-quality applications in Western Europe whereby the depicted production quantities relate to 2016. The additional utilisation quantities from stockpiles etc. are also shown. The total quantity concerned is approx. 26.8 Mta. Of this, 4.6 Mta (17.2 %) are used as concrete admixture. Another 3.8 Mta are used in the cement industry for the production of ash cements or as raw material in the clinker production process. In Germany, as one of the leading countries, information from the Wirtschaftsverband Mineralische Nebenprodukte e.V. (industry association for mineral secondary products) shows that about ¾ of the produced quantities of hard coal fly ash are certified in accordance with DIN EN 450-1, have building inspectorate approval as a concrete additive according to DIN EN 2006-1 and are also utilised accordingly. The remaining quarter is used in cement production, in earthworks and road construction and for other purposes, so that the utilisation rate is almost 100 %.
The utilisation of fly ash and bottom ash has become an economic factor. Numerous service providers (Fig. 11) have established themselves on the market in order to sell these by-products of the power generation industry as high-quality and versatile raw materials, especially for the cement and concrete industries. With falling production volumes in Europe and the USA, previously less exploited supply markets in Asian countries are now also in focus. Taking the example of the USA, Fig. 12 illustrates how the production rates of ash from coal-fired power plants and the corresponding utilisation quantities in the building materials industry have changed in recent years. It shows that from 2013 to 2017 the produced quantity of ash fell by 28.5 %, but the amounts utilised have increased by 27.2 %, from 14.7 Mta to 18.7 Mta, despite the falling production volumes. The proportion of ashes used for blended cements increased by 100 %.
4 Use of FGD gypsum
In the wet flue gas desulphurisation process, the filtered flue gases are desulfurised in downstream systems (FGD) by injecting suspensions of limestone or hydrated lime. The lime reacts with the SO2 present in the flue gas to form CaSO4.2H2O (calcium sulfate dihydrate or FGD gypsum). FGD gypsum does not differ in its chemical composition from natural gypsum.
FGD gypsum is used largely in the gypsum industry for the production of building materials such as plasterboard, gypsum plaster or gypsum floor screed. FGD gypsum can also be used in the cement production process, added in a proportion of up to 5 % as a setting regulator instead of natural gypsum or anhydrite. Further fields of application concern its use in agriculture as fertilizers or soil conditioners and in the production of hemihydrate and anhydride. The gypsum from modern FGDs is of such good quality and purity, and has such a low content of pollutants, that it can replace natural gypsum in building material applications.
According to World Mining Data, the global production of mined natural gypsum amounted to 151.3 Mta in 2017 (Fig. 13). The developed countries in Europe and America account for 31.5 % of this, as these countries also have the largest capacity for the production of plasterboard [5]. According to a report by Smithers Apex, the global market in 2016 for natural gypsum and synthetic gypsum totalled 252 Mta, of which about 101 Mta concerned synthetic gypsum. More than 95 % of the synthetic gypsum is FGD gypsum, while the remaining quantities come from the production of hydrofluoric acid, phosphoric acid, citric acid and dilute acid (titanium dioxide production). About 90 % of the FGD gypsum is produced in Europe, the USA and China. In principle, the future of FGD gypsum is subject to the same conditions as fly ash from coal-fired power plants. However, FGD gypsum in good purity and quality is also produced by lignite-fired power plants.
Fig. 14 shows a plasterboard factory in the USA. The plant is located directly adjacent to a coal-fired power plant and uses 100 % FGD gypsum as a raw material instead of natural gypsum. In Europe and China, there are also numerous plasterboard plants using 100 % or nearly 100 % FGD gypsum. Knauf, the world leader in the gypsum industry, uses nearly 60 % synthetic gypsum in its European factories, while the proportion of natural gypsum has fallen below 40 % over the years, while recycled gypsum now accounts for nearly 5 % of its production. Other leading manufacturers of gypsum plasterboard such as Saint Gobain and the Etex Group in Europe, or USG Corp., National Gypsum Georgia-Pacific and CertainTeed in North America, or BNBM and Taishan Gypsum in China, use similarly high quantities of FGD gypsum in their production processes.
In Western Europe (EU15), a total of 9.531 Mta FGD gypsum was produced in 2016. The quantities for the EU28 are estimated to exceed 21 Mta. Of the production volumes in Western Europe (Fig. 15), 4.17 Mta (43.7 %) went into plasterboard production, and 2.42 Mta (25.3 %) were utilised for other gypsum products, such as gypsum plaster, self levelling floor screeds etc. The amount going to the cement production industry was 5.6 %. However, a large amount (25.4 %) was not used directly, but served as backfill material or went to landfill sites. The situation in the USA is not entirely comparable but similar (Fig. 16). Of the USA’s much larger production quantity of FGD gypsum, totalling 32.7 Mta in 2017, the large amount of 15.86 Mta (48.5 %) went into plasterboard production (although other gypsum products are probably also included in this quantity), while 2.32 Mta (7.1 %) went into cement production and 30.7 % were used for backfilling or landfilling.
5 Prospects
The supply of iron and steel slags is expected to be assured in the future. However, the level of demand from the global cement industry will increase, particularly because the worldwide trend for reduction of the clinker factor in cement production will cause a decrease from the current level of more than 70 % to less than 60 % by 2030 due to the CO2 problem. Significant decreases in the available quantities of by-products from coal-fired power plants are already being felt, especially in Europe and the USA. This concerns the supply of both high-quality fly ash and FGD gypsum. For this reason, efforts are already under way in the USA to process fly ash from previous wet-ash power plants. Estimates assume that this could produce several 100 Mta of fly ash. In Europe, the future quantities of FGD gypsum are also threatened [6]. Instead of more than 20 Mta, it is possible that only 4.6 Mta could be available in 2050.
Literatur • Literature:
[1] Ueki, Y.: History and Utilization of Portland Blast Furnace Slag Cement. NIPPON STEEL & SUMITOMO METAL TECHNICAL REPORT No. 109, July 2015, pp. 109-113
[2] Hamm, H.; Müller, R.: Das zweistufige Knauf-Research-Cottrell-Verfahren zur Rauchgasentschwefelung am Beispiel des Kraftwerkes Franken. ZKG 6/1982, pp. 313-317
[3] CEMBUREAU: Cements for a low-carbon Europe. The European Cement Association. November 2012, Brussels/Belgium
[4] Harder, J.: Development of Clinker Substitutes. ZKG 4/2019, pp. 42-51
[5] Harder, J.: Global Trends in the Gypsum Industry. ZKG 9/2019, pp. 29-36
[6] Demmich, J.: The Future of FGD Gypsum in Europe, 25th ASHTRANS Europe Conference 2015, 7-8 September 2015, Copenhagen/Denmark
Autor/Author:
Dr.-Ing. Joachim Harder
OneStone Consulting Ltd.
Varna/Bulgarien
Joachim Harder studierte Verfahrenstechnik an der TU Braunschweig und promovierte dort. Nach mehr als 10 Jahren Industrietätigkeit in verschiedenen Managementfunktionen gründete er 1997 die Beratungsfirma OneStone Consulting. Dr. Harder ist ein anerkannter Experte im internationalen Marketing mit dem Schwerpunkt Marktanalysen für Geschäftsfeldstrategien.
Er ist Autor diverser Publikationen und gefragter Redner auf internationalen Konferenzen.