Recovery and recycling of dumpsite materials
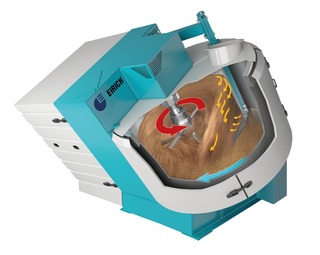
© Eirich During the smelting of raw ore materials, dusts are produced that still contain small amounts of metals. In the past, these dusts were dumped in overground storage sites. For a long time it was not a commercially viable proposition to recover the remaining metals from these waste materials, partly because of the relatively low metal prices. However, changes to the law mean that it will in future no longer be possible to dump this waste above ground. Combined with the significantly higher metal prices today, recovery and recycling of the dusts that are continuously produced, but also of the dumped dusts, is an economically interesting alternative to underground dumping. EIRICH’s dispersing and drying technology enables economical processing.
2 Plant for the preparation of fly ash with an EIRICH mixer
© Eirich
Everything feasible in a single mixer: For a multi-stage hydrometallurgical process, which, for example, treats waste materials from the smelting of heavy metals, a suspension is first produced from the dumped residues. Inert coarse particles are separated after suspension and thus do not unnecessarily burden the further treatment process. At the end of the process chain, in the same mixer using hot gas a filter cake is convectively dried and granulated dust-free. The granulate is then fed into the smelting process. For high throughput capacities, customers also use two independent mixers at the beginning and end of the process chain.
The unique operating principle of the mixer is based on a rotating pan that transports the material being mixed, and a variable-speed mixing tool known as the rotor, which can run from slow to fast speeds. The separation between material transport and the mixing process allows the speed of the mixing tool (and thus the power input into the mix) to be varied within wide limits. And: the mixer is suitable both for mixing as well as for granulating, kneading and dispersing. With the matching accessories, the mixer can also be used for convection drying.
The dispersing of earth-moist dumpsite materials in an Eirich MixSolver® is a method that has already been successfully established for decades in other industries. In the ceramic industry, for example, this method has been used to replace the complex process for slip preparation from pit-wet clay using ball mills and stirring containers. Alongside spray/casting slips for tiles, utility ceramics and technical ceramics, the Eirich MixSolver® is also used to produce coating pigments for paper manufacturing, coal/water suspensions, foamed concrete, microsilica or pigment suspensions, as well as road marking compounds. The machines are available in sizes from 1 to 7000 l. In comparison to preparation in mills or stirrers, thanks to the significantly higher power input the preparation times can be noticeably reduced, into the range of 10 to 15 minutes. Thanks to the rotating container, the raw materials are continuously fed to the dispersing tool, so there are no zones without circulation, which can be a problem with conventional stirring vessels.
The energy savings in comparison to ball mills will be significantly above 50 %. In addition, the Eirich MixSolver® technology also permits simple separation of non-soluble foreign substances containing no recyclable materials downstream, which are otherwise ground together with the recyclable materials and place an unnecessary burden on the process.
Drying and granulating in Eirich mixers is also widespread in many industries. In the preparation process e. g. a filter cake with material moisture of around 20 % is produced. The process of drying (with hot air) and granulating filter cakes into a dust-free granulate with good flowing and storage properties – often still with a defined range of grain sizes – is a challenging task, but one that Eirich has already met in the past in many similar tasks. Conventional drying technology often meets its limits here, e.g. because material becomes deposited on the slow-running tool or on hot surfaces, as is familiar from thin film dryers. But these things are not a problem for the Eirich mixer.
On sizes from 1 to 3000 l, the mixer used for drying and granulating only has one single moving mixing tool. In addition, it does not require fast-running and filigree scraping tools which are exposed to intensive wear on the wall. The rotor, which is mounted with sufficient distance to the wall, can run freely in the material at tool speeds of up to more than 30 m/s – depending on the task and required grain size. Varying the speed can have a considerable influence on the grain spectrum; granules with a d50 value ranging from 1 – 5 mm are possible, depending on the material. The movement of material in the mixer corresponds to a mechanically generated fluid bed, with optimally sized exposed granulate surfaces – ideal for an efficient drying process with hot air, which is directed into the mixer.
In recent years, Eirich has supplied several mixing plants for the recovery of recyclable materials from dumpsite waste materials, e.g. MixSolver® units in the size RLV24 (capacity: 3000 l) as well as drying lines based on mixers of size RV19 (capacity 1500 l), mostly in corrosion-resistant design, with all parts that come into contact with product being made of stainless steel. The flexibility of the Eirich technology also allows the process parameters to be adapted to changing waste materials so that the plant can always be operated at maximum efficiency. In the example described, this enables the customer to increasingly cover the demand for high-priced heavy metals by means of recycling.